Our Products HydroEROsive Machining
hSonplas offers extensive expertise and concepts for hydroerosive machining
In HydroEROsive machining—or HERO for short—a liquid mixed with abrasive particles is pumped through the inner geometry of a workpiece under high pressure. This type of flow grinding enables the deburring, rounding, and calibration of bore flow for components across various industries. The process meets all drawing and component specifications. We offer extensive expertise, including in the design of systems and machines.
For which specific applications is the HERO process particularly suitable?
One process, three possibilities:
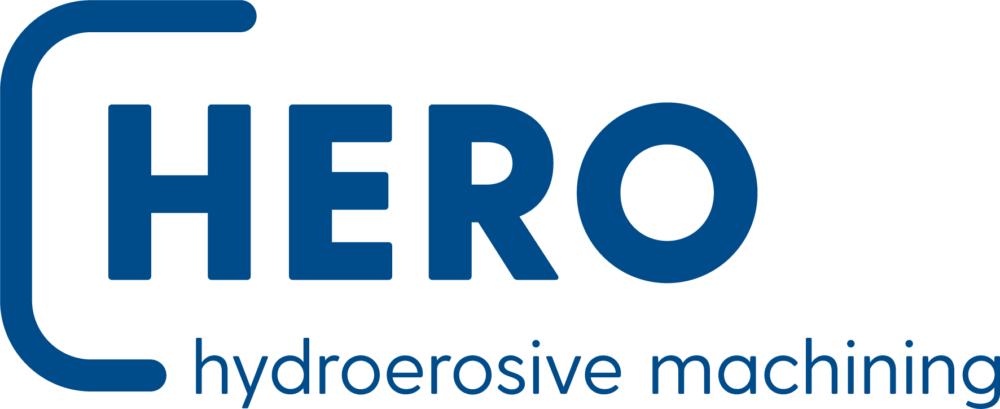
With HERO machining, you can efficiently and precisely remove internal burrs in a controlled manner. This may be necessary to ensure the functionality of a component, but also to improve ergonomics or aesthetics.
- Before HERO
- After HERO
The process also enables you to smooth and round bore intersections, ensuring consistent performance throughout the component’s service life. It improves high-pressure resistance, meaning the component will not wear or will wear significantly more slowly even under high pressures. Additionally, it mimics an artificial pre-aging process for the component. The HERO process is also capable of machining complexly shaped workpieces.
Due to the low viscosity of the process medium used, the method is also well-suited for flow calibration of bores. Throughout the entire process, you can monitor the increasing flow rate of the component and stop precisely at the desired value. This enables you to achieve flow tolerances of ±1% with high process reliability.
Contact us!
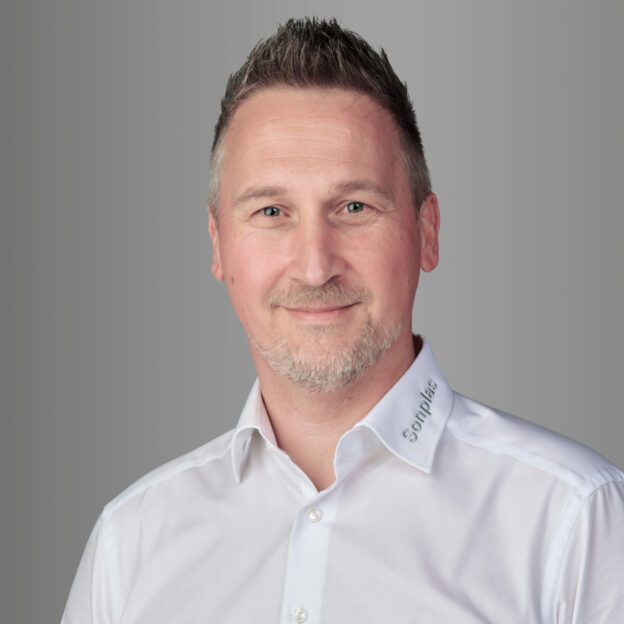
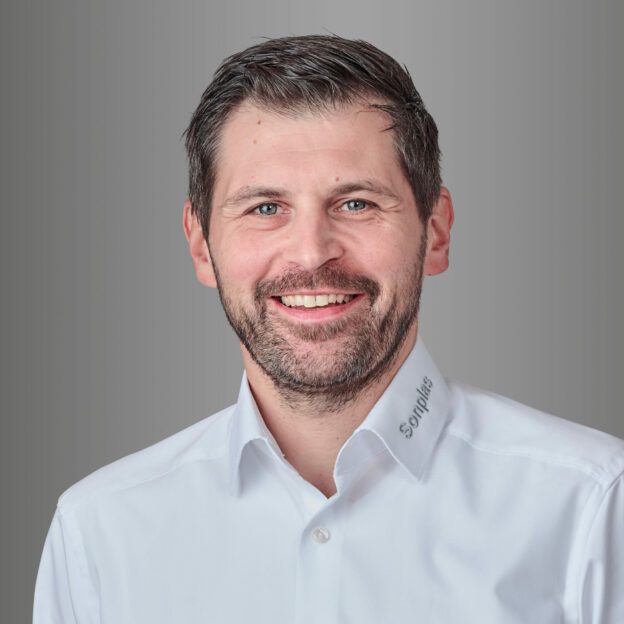
More about the HERO Process
How does the HERO process work?
The fluid containing abrasive particles flows through the component along internal bore intersections or geometries. The rounding effect occurs as these particles are accelerated by the narrowing of a cross-section—when one bore transitions into another with a smaller diameter. As a result, the particles achieve high kinetic energy and, due to the focused flow, strike the walls or edges of the bore at high speed. This process effectively removes material.
The perfect process medium
To achieve the desired flow rates, geometries, and rounding degrees, the optimal rheological specification of the process medium must be defined. Depending on the application, the media are formulated as either mineral oil-based or water-based and adjusted to viscosities ranging from 0.5 to several 10,000 mPa·s (millipascal seconds). Boron carbide, a highly abrasive ceramic, is used as the abrasive particle. Additionally, the grinding fluids are specifically formulated with additives to provide effective corrosion protection for the components being processed.
For which components is the HERO process suitable?
You can use the HERO process for a wide variety of components, with the bore size being a crucial factor. Our systems can hydroerosively machine holes with diameters ranging from 0.1 to 5 millimeters. The workpieces can be made from materials such as steel, stainless steel, aluminum, nickel-chromium-based superalloy, and precious metals like gold, silver, or platinum. Additionally, we can process hard metals, glass, ceramics, plastics, and fiber-reinforced composites. Many other materials can also be accommodated. Please feel free to reach out to us.
The HERO process is especially relevant for these sectors
- Automotive industry
- Aerospace industry
- Chemical engineering
- Agriculture
- Medical technology
- Semiconductor industry
- Environmental technology
- Electrical industry
- Food industry
- Creative and design industries
- Maritime industry
- Mechanical engineering and metal processing
- Wind energy
And many other sectors. Don’t hesitate to get in touch with us.
What is special about HERO?
Thanks to its excellent wetting properties and compatibility with rinsing and testing fluids, the process medium can effortlessly remove particles. Depending on requirements, the desired cleanliness classes according to VDA19/ISO16232 can be met. The water-based process medium, in particular, offers several advantages: it is hygienic and has a low carbon footprint.
With the HERO process, you can precisely calibrate the flow rate of a component. We select the optimal fluid based on the specific part requirements. The operator can continuously monitor the increasing flow rate in real time, make precise adjustments to meet the required value, and reliably set flow tolerances throughout the process.
At your request, we can equip the systems with rotary tables, enabling processes such as hydroerosive machining, rinsing, and/or flow measurement to run in parallel. Customize the special machine modularly to suit your specific requirements. Process stations like rinsing or measuring devices can also be integrated at a later stage. Additionally, databases and MES systems can be seamlessly connected. Component markings (DMC) ensure complete traceability of machining and process data. Flow control and master parts are also available, with integrated software feeding these components into the process in a specific cycle and performing regular checks to maintain accuracy and reliability.
Because our systems are closed systems, operating errors are eliminated in the HERO process. The user only needs to manually load the machine or change the pallets as needed. For higher quantities, automatic loading is available, such as with a robot loading module. This enables seamless integration of processes. The loading module can be positioned, for instance, after erosion or laser drilling and before HERO processing.
Depending on your requirements, we can provide you with a simple developing machine or a system designed for large-scale production. As a trusted partner, we have been offering unique solutions for our customers’ demands for over 30 years.
FAQ
What are the advantages of hydroerosive machining?
The process can also be applied to particularly hard materials. With hydroerosive machining, you can precisely round bore intersections without impacting mating surfaces. Additionally, it is ideal for reliably calibrating the flow of bores. The process offers versatility in terms of material choice and shape complexity, making it suitable for a wide range of applications.
How does hydroerosive machining differ from other machining processes?
Hydroerosive machining primarily relies on the abrasive action of the process medium, whereas techniques like grinding or polishing focus more on creating smooth, mirror-like surfaces. The HERO process excels in removing burrs from internal bore intersections that mechanical methods cannot reach or access. This enables precise machining of complex internal geometries while maintaining the integrity of mating surfaces and ensuring high process reliability.